work in process inventory balance formula
Ending work in process. The last quarters ending work in process inventory stands at 10000.
Inventory Raw Materials Work In Progress And Finished Goods
During April the following costs appeared in the Work in Process Inventory account.
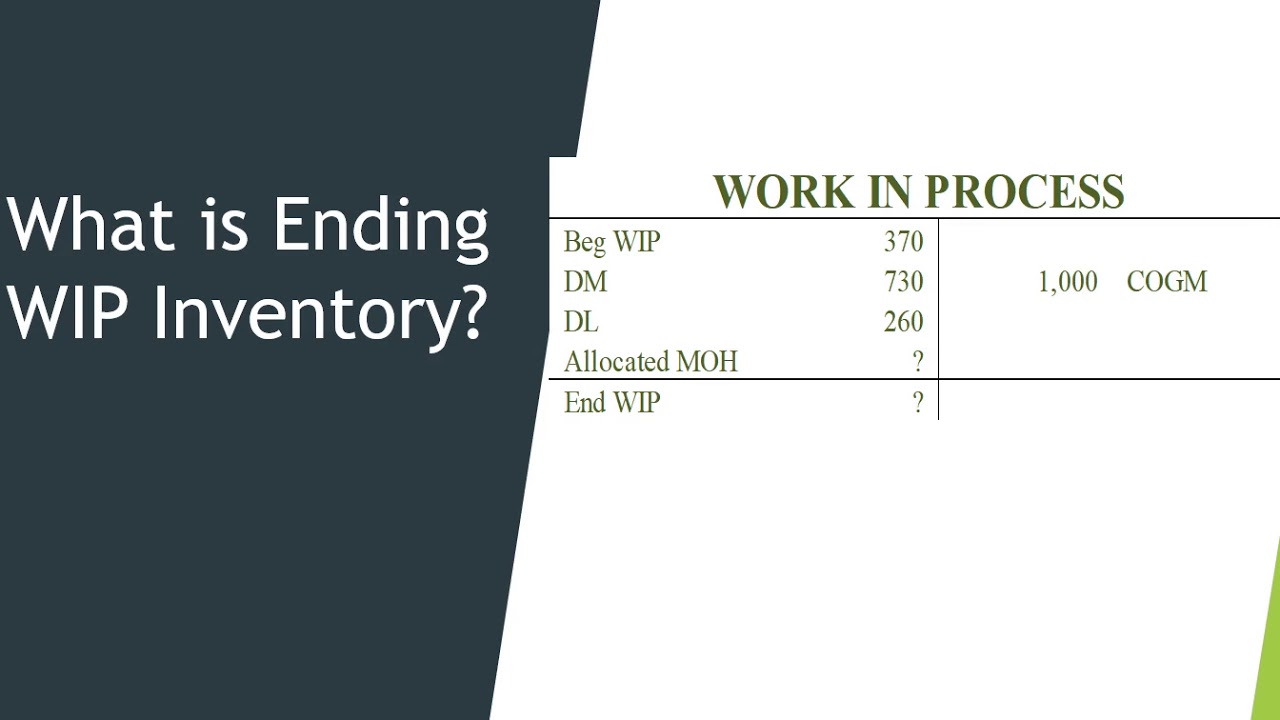
. Beginning WIP Manufacturing costs - Cost of goods manufactured. WIPs are considered to be a current asset on the balance sheet. The term work in process WIP inventory is widely spread and mainly used in the sphere of supply chain management.
Below is the data table. The factory overhead costs can be calculated for the accounting period. WIP is calculated as a sum of WIP inventory total direct labor costs and allocated overhead costs.
Furthermore what does work in process mean. Production costs include raw materials labor used in making goods and allocated overhead. This product value is important for financial reporting.
It relates to the overall costs of those goods that are non-finished yet or still in production. As determined by previous accounting records your companys beginning WIP is 115000. Imagine BlueCart Coffee Co.
The more WIP inventory that goes through the production process the higher the raw materials and labor costs will be which will impact the total costs of manufactured goods. WIP Inventory Example 2. In this case for example consider any manufactured goods as work in process.
Beginning work in process inventory cost The beginning WIP inventory cost refers to the previous accounting periods asset section of the balance sheet. The manufacturing costs incurred in this quarter are 200000 and the cost of manufactured goods is 100000. WIP inventory includes the cost of raw materials labor and overhead costs needed to manufacture a finished product.
During the remaining financial year the company has made purchases amounting 20000 and during that time on the companys income statement the cost of goods sold is 40000. The WIP figure indicates your company has 60000. The formula is as followed.
Raw Materials Direct Labor Costs Manufacturing Overhead Manufacturing Costs. Charleston Company uses a job-order costing system. Beginning WIP Inventory Manufacturing Costs COGM Ending WIP Inventory.
Work-in-process is an asset and so is aggregated into the inventory line item on the balance sheet usually being the smallest of the three main inventory. During the year 150000 is spent on manufacturing costs along with your total cost of finished goods being 205000. The work-in-process inventory that a company has started but not completed has specific value.
Deduct the cost of raw material from this figure that is on hand at the end of the accounting period to determine the costs of materials consumed during the accounting period. A work-in-progress WIP is the cost of unfinished goods in the manufacturing process including labor raw materials and overhead. Work-in-process is an asset and so is aggregated into the inventory line item on the balance sheet usually being the smallest of the three main inventory accounts of which the others are raw materials and finished goods.
Work in process WIP inventory refers to materials that are waiting to be assembled and sold. The beginning WIP inventory cost refers to the previous accounting periods asset section of the balance sheet. Company As ending WIP inventory for this quarter is.
Lets calculate Company As ending WIP inventory as per the formula. Inventory Formula Example 1. WIP is a concept used to describe the flow of manufacturing costs from one area of production to the next and the balance in WIP represents all production costs incurred for partially completed goods.
Under this method the cost of completed units is. For example a restaurant uses the three cost line items mentioned above to transform raw. Work in process inventory formula.
The work in process formula is the beginning work in process amount plus manufacturing costs minus the cost of. From which we can derive a basic formula for calculating WIP inventory costs. It is generally considered a manufacturing best practice to minimize the amount of work-in-process in the production area.
Cost of manufactured goods. Once you sell the finished goods transfer the. As per the Merriam-Webster dictionary Work-in-process WIP refers to a component of a companys inventory that is partially completed.
This leaves the company with an ending WIP inventory balance of 4500. WIP inventory is a vital production step that is considered an asset on a companys balance sheet. The amount of ending work in process must be derived as part of the period-end closing process and is also useful for tracking the volume of production activity.
The labor costs for the accounting period should be calculated. To calculate the beginning WIP inventory determine the ending WIPs inventory from the previous period and carry it over as the beginning figure for the new financial period. The value of that partially completed inventory is sometimes also called goods in process on the balance sheet particularly if the company is manufacturing tangible items rather than providing services.
Let say company A has an opening inventory balance of 50000 for the month of July. And C c cost of goods completed. Work In-process Inventory Example.
Definition formula and benefits. A work in process or WIP for short is the term that refers to any inventory thats been initiated into production but hasnt been completed by the end of a companys accounting cycle. The value of the partially completed inventory is sometimes also called goods in process on the balance sheet.
Beginning balance 24000 Direct material used 70000 Direct l. Work in process WIP work in progress WIP goods in process or in- process inventory are a companys partially finished goods waiting for completion and eventual. The work in process formula is the beginning work in process amount plus manufacturing costs minus the cost of manufactured goods.
The calculation of ending work in process is. Since WIP inventory takes up space and cant be sold for a profit its generally a best. The balance represents manufacturing costs of unfinished production at the end of the period.
Amount of work-in-process inventory available at the end of the account period.
Use The Job Order Costing Method To Trace The Flow Of Product Costs Through The Inventory Accounts Principles Of Accounting Volume 2 Managerial Accounting
Inventory Formula Inventory Calculator Excel Template
Cost Of Goods Manufactured Formula Examples With Excel Template
Ending Inventory Formula Step By Step Calculation Examples
What Is A Work In Progress Wip 2020 Robinhood
Manufacturing And Non Manufacturing Costs Online Accounting Tutorial Questions Simplestudies Com
Work In Process Inventory Formula Wip Inventory Definition
Ending Inventory Formula Calculator Excel Template
Work In Process Wip Inventory Youtube
Wip Inventory Definition Examples Of Work In Progress Inventory
Average Inventory Formula How To Calculate With Examples
Ending Inventory Formula Step By Step Calculation Examples
Cost Of Goods Manufactured Formula Examples With Excel Template
Ending Work In Process Double Entry Bookkeeping
How To Calculate Finished Goods Inventory
What Is Work In Process Wip Inventory How To Calculate It Ware2go